Un despegue con inspección del borde delantero
MTU Aero Engines recurre a PolyWorks|Inspector™ para optimizar sus procesos de inspección
Cuando se vuela a 30,000 pies en el aire a una velocidad de 550 mph, se comprende más que nunca la importancia de contar con un motor a reacción confiable. MTU Aero Engines, el principal fabricante de motores a reacción de Alemania, se preocupa por su seguridad. La filial de Daimler/Chrysler ha establecido rigurosos procesos de inspección en cada fase de su ciclo de desarrollo/fabricación de productos para garantizar la calidad total de sus productos. Para optimizar y aumentar el alcance de sus técnicas de inspección, MTU ha recurrido a PolyWorks|Inspector, la solución de software de inspección de nubes de puntos líder en el mundo. Descubra cómo PolyWorks|Inspector ha reducido significativamente el tiempo de inspección de los álabes de las turbinas de MTU en más del 85% y simultáneamente proporciona a los ingenieros de calidad más información que nunca sobre la calidad de las piezas.
El desafío
MTU - Propulsión del mundo
MTU Aero Engines GmbH es el desarrollador, fabricante y proveedor de servicios de desarrollo de reparación de componentes, ensamblajes y turbinas de gas industriales de motores aeronáuticos civiles y militares líder en Alemania.
La empresa participa en proyectos de cooperación en curso con los principales integradores y fabricantes de sistemas del mundo, incluidos Pratt & Whitney, General Electric, Rolls-Royce, Snecma, Volvo y FiatAvio.
MTU es reconocido por su enfoque de alta tecnología en todo lo relacionado con sus motores. Utiliza tecnologías de vanguardia en el desarrollo, la fabricación y la inspección por igual. “Esto nos permite ofrecer a nuestros clientes los productos avanzados de alta calidad que tienen derecho a esperar”, dijo el Dr. Karl-Heinz Dusel, ingeniero de calidad de MTU.
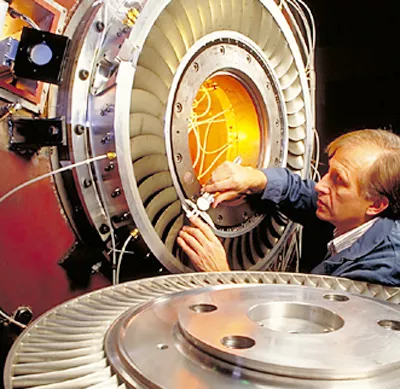
La complejidad de un motor a reacción
Un motor a reacción está compuesto por cientos de componentes que deben inspeccionarse de cerca antes del ensamblaje. Los procesos de inspección que MTU ha utilizado tradicionalmente han demostrado provocar cuellos de botella en el ciclo de producción debido a la lentitud y complejidad de las técnicas empleadas. Además de la limitación de la velocidad, los equipos de inspección, como las máquinas de medición de coordenadas (MMC), tienen un alcance restringido, lo que obliga a los ingenieros de calidad a concentrarse en las características limitadas de una pieza y los priva de información valiosa.
Los motores a reacción se utilizan para impulsar los aviones. Para despegar y volar por el cielo, el motor a reacción de un avión produce gases de escape que salen disparados por la parte trasera del motor. Para crear esa tremenda energía (empuje), el motor ingiere aire para la combustión usando su ventilador en la parte delantera. El compresor comprime el aire y lo fuerza a la cámara de combustión. El combustible se inyecta y se mezcla con el aire comprimido entrante y la mezcla de aire y combustible se quema continuamente. El calor resultante expande el gas a un múltiplo de su volumen, lo que hace que escape de la cámara de combustión en una corriente de alta energía. Luego, el gas corre a través de los álabes de la turbina, hace que giren y produzcan la energía necesaria para impulsar el compresor y el ventilador.
Las turbinas consisten en varias etapas, cada una de las cuales emplea una fila de álabes guía fijos y una fila de álabes móviles. Los álabes, aunque estén al rojo vivo, deben tener la suficiente fuerza para soportar las cargas centrífugas debido a la rotación a altas velocidades. ¡Bajo tales condiciones, no se permiten imperfecciones! Cada pieza debe cumplir las especificaciones de diseño más estrictas.
Procesos de inspección tradicionales
MTU tradicionalmente ha utilizado procesos de inspección basados en CMM para medir los álabes. Este proceso aumenta significativamente el tiempo que toma el proceso de fabricación:
- El proceso de adquisición de datos de CMM tarda hasta 80 minutos para cada álabe.
- No es posible escanear el álabe en el sitio durante el proceso de fabricación, por lo que se requiere que MTU lleve las piezas a la estación de digitalización.
- El número de puntos medidos es limitado (cien puntos), lo que hace imposible la inspección global de la superficie.
- Operar una CMM es una tarea que requiere mucho tiempo y requiere la supervisión continua de técnicos altamente capacitados.
- El procesamiento de datos, las mediciones, las comparaciones y la generación de informes son procesos largos y requieren varios paquetes de software.
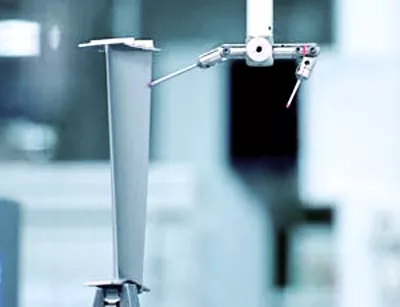
La solución
Rompemos la barrera del sonido con PolyWorks|Inspector
Para garantizar la calidad de todos sus productos, MTU trabajó en estrecha colaboración con Duwe 3d, un proveedor y distribuidor de soluciones de digitalización 3D de bordes delanteros de PolyWorks en Alemania, para desarrollar una solución de inspección personalizada adaptada a los requerimientos más estrictos de la industria aeroespacial.
MTU ahora se beneficia de las numerosas ventajas de utilizar un sistema de escáner láser 3D junto con PolyWorks como parte de sus procesos de control de calidad. Para la inspección de los álabes de la turbina, MTU utiliza un escáner láser montado en brazos articulados (FARO GoldArm y ModelMaker de 3DScanners) para escanear piezas directamente en el sitio y capturar cada entidad geométrica, incluidas las que se encuentran en áreas ocultas.
Esta nueva técnica de inspección ha permitido a MTU reducir drásticamente el tiempo para adquirir y procesar nubes de puntos de sus álabes de turbina: “Una gran ventaja de PolyWorks es su flexibilidad para adaptarse a cualquier tipo de sistema de digitalización”, declaró el Dr. Dusel. “Esto nos da la libertad de experimentar e identificar la solución que mejor se adapte a nuestros requerimientos. Además de este gran ahorro de tiempo, la inspección de nubes de puntos de alta densidad con PolyWorks nos brinda la posibilidad de aplicar muchas aplicaciones de medición nuevas.”
Inspección global de la superficie
Antes de analizar áreas específicas de los álabes de la turbina, MTU evalúa globalmente la calidad de la pieza fabricada comparando cada punto digitalizado con su punto de referencia subyacente (objeto CAD). Los ingenieros de calidad establecen las tolerancias correspondientes y se genera un mapa de color para ilustrar la magnitud de las desviaciones. Esta técnica proporciona una descripción general rápida de la calidad general de la pieza y permite a los especialistas centrarse en áreas fuera de las tolerancias predeterminadas para un análisis más detallado. Las técnicas de inspección tradicionales basadas en CMM no pueden proporcionar información tan valiosa a los ingenieros de calidad. Las poderosas capacidades de comparación de PolyWorks no solo identifican las deformidades de una pieza, sino que también ayudan a los ingenieros de calidad a identificar la fuente del problema a lo largo del proceso de fabricación y corregirlo.
Las técnicas de comparación de punto a CAD de PolyWorks son totalmente personalizables y más precisas que cualquier otra solución de software de procesamiento de nubes de puntos en el mercado.
Análisis de perfil
Los perfiles son la geometría más importante de un álabe, ya que tienen un impacto directo en el flujo de gas. Las secciones transversales se utilizan para calcular la aerodinámica de cada álabe.
El análisis de perfil se realiza utilizando las sofisticadas capacidades de análisis transversal de PolyWorks. Una sección transversal de una pieza es un perfil en 2D que se obtiene intersecando un plano con la superficie del objeto; es una “rebanada” del objeto. Para cada corte en rebanada, se crea un perfil de datos y un perfil de referencia (CAD). Para obtener un análisis preciso de cada perfil, PolyWorks ofrece capacidades de alineación local (mejor ajuste local).
Los mapas de color de sección transversal se generan de acuerdo con las tolerancias definidas por el usuario. PolyWorks también muestra bandas de tolerancia junto con CAD y perfiles de datos.
Una ventaja importante de PolyWorks es su capacidad para proporcionar las desviaciones “reales”, independientemente del ángulo entre las secciones transversales y la normal de una superficie.
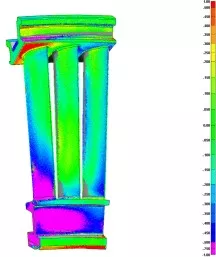
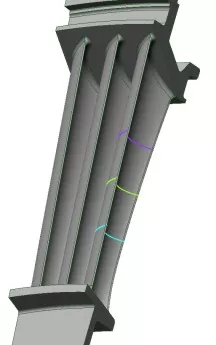
Inspección de bordes delanteros: Galgas virtuales
PolyWorks ofrece capacidades de galgas virtuales únicas mediante calibradores 3D. Estas herramientas son cilindros sólidos que se colocan en el espacio 3D y se extienden hasta que llegan a un punto, un triángulo o una superficie NURBS. En este caso, se utilizan calibradores para obtener la posición exacta de puntos estratégicos en el “borde delantero” de los álabes. El borde delantero es un factor esencial que influye en la aerodinámica del flujo de gas.
“PolyWorks replica virtualmente los procesos típicos de inspección de galgas físicas”, dijo el Dr. Dusel. “Las capacidades de galgas de PolyWorks nos ofrecen valiosa información sobre el borde delantero en una fracción del tiempo de nuestro método de medición física tradicional y, al mismo tiempo, conservan la misma exactitud y precisión.”
Deje que el piloto automático tome el control
“Con PolyWorks, estamos en el asiento del piloto”, dijo el Dr. Dusel. “PolyWorks le permite definir sus propias tolerancias y le brinda una retroalimentación constante para monitorear sus operaciones. Con la capacidad avanzada del lenguaje de programación de macros de PolyWorks, podemos programar fácilmente secuencias de inspección completas, desde la primera alineación hasta el informe final, en solo unos minutos. Luego, encendemos el dispositivo con piloto automático y dejamos que PolyWorks realice un proceso de inspección completo con solo un clic del ratón utilizando nuestras propias especificaciones.”
Los beneficios
Los beneficios que se observan al usar PolyWorks son:
- Proporciona más información a los ingenieros de calidad y reduce el tiempo de análisis de datos, cálculo, etc.
- Aumenta la cantidad de piezas que se inspeccionan, con lo cual se mejora aún más la calidad y confiabilidad general del producto
- Permite a los usuarios realizar mediciones a nivel global (pieza completa), y no solo áreas específicas como con una CMM
- Reduce los cuellos de botella en los centros de inspección centralizados, con lo cual se disminuye el tiempo de inactividad en la línea de producción